Pressure Gauge Calibration
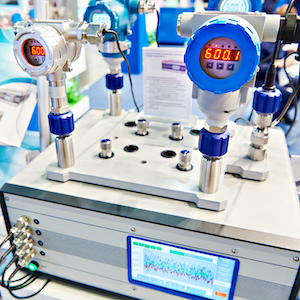
Figure 1: Digital pressure gauge calibration
Pressure gauge calibration is the process of verifying the accuracy of a pressure gauge against a known standard. This is done by comparing the output of the gauge to a reference gauge or by applying a known pressure to the gauge and measuring its output. Calibration can be performed on a variety of different types of pressure gauges, including analog and digital gauges, and is an important step in ensuring that the gauge is providing accurate and reliable readings. The process of calibrating a pressure gauge typically involves adjusting the gauge so that it is in compliance with industry standards and regulations.
Table of contents
- How to calibrate a pressure gauge
- Factors to consider for pressure gauge calibration
- In-house vs outsourcing calibration
- FAQs
View our online selection of pressure gauges!
How to calibrate a pressure gauge
Calibrating a pressure gauge is done with pressure calibration equipment like a deadweight tester, standard pneumatic calibrator, or any other pressure gauge calibrator with an accurate reading. No matter the tool, the general principles and steps to calibrate a pressure gauge are very similar, whether it’s mechanical or digital gauge calibration. The following steps describe the use of a hand pump calibrator (Figure 2).
- Connect the hand pump calibrator to the pressure gauge to be calibrated using the appropriate adapter or fitting.
- Set the desired pressure on the hand pump calibrator.
- Slowly pump the hand pump calibrator until the desired pressure is reached.
- Observe the pressure gauge and ensure that it reads the same pressure as the hand pump calibrator.
- If the gauge does not read the correct pressure, adjust it according to the manufacturer's instructions.
- Repeat the process at multiple pressure points to ensure the gauge is accurate throughout its range.
- Record the results of the calibration and make any necessary adjustments.
- Once calibration is complete, disconnect the hand pump calibrator and store it properly.
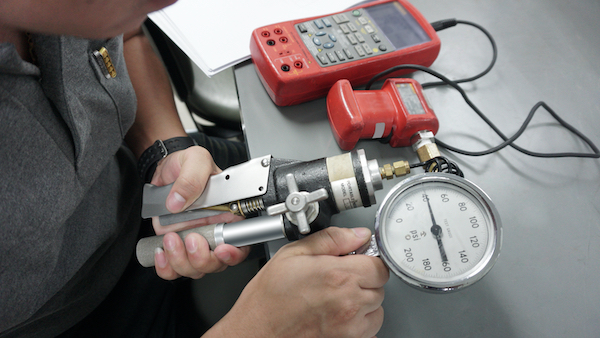
Figure 2: Hand pump for pressure gauge calibration. This device offers a simple yet effective way to quickly calibrate a pressure gauge.
Factors to consider for pressure gauge calibration
Pressure calibration is done utilizing an accurate pressure system. The pressure measurement on calibrated pressure gauges is documented and compared with the uncalibrated gauge to identify the margin of error. However, many factors can affect the calibration process and should be considered:
Accuracy class
The accuracy class is the maximum margin of error permissible for the pressure gauge for the maximum scale reading. During calibration, the accuracy class will help operators know the acceptable margin of error. Table 1 helps identify the permissible error margin based on the pressure gauge’s accuracy class.
Table 1: Permissible error margin based on the pressure gauge’s accuracy class
Accuracy class | Permissible error margin |
0.1 | 0.1% |
0.25 | 0.25% |
0.6 | 0.6% |
1 | 1.0% |
1.6 | 1.6% |
2.5 | 2.5% |
4 | 4.0% |
Pressure media
When calibrating a pressure gauge, it is ideal to use the same media that is in the system that the pressure gauge attaches to. If this is not possible, for low-pressure gauges, calibration with air/gas is suitable while liquids are safer for high pressure gauges.
Contamination
Contamination like dirt, moisture, or grease can damage the pressure gauge as well as the calibration device. Thus, it is necessary to make sure the media and equipment are free of contamination and don't disrupt the operation.
Height difference
During calibration, the difference in height between the pressure gauge calibration equipment and the pressure gauge can cause an error because of the hydrostatic pressure of the media. This is mostly observed in liquid media and not gas media. The magnitude of the error differs depending on the density of the liquid as well as the difference in height. If it is not possible to put the calibration equipment and gauge at the same height, the effect of the height difference should be taken into account during calibration. A 2.5 cm (1 in) height difference accounts for an approximately 0.02 bar (0.3 psi) pressure reading inaccuracy.

Figure 3: Electronic pressure calibration devices are typically used in dedicated pressure equipment calibration laboratories.
Leak testing
A leak test is crucial before calibration as any leakage in the pipe system can cause errors during calibration. The leak test can be done by pressurizing the system, letting the pressure gauge stabilize, and monitoring the pressure. Any drop in pressure can indicate leakage. It is necessary to ensure the pressure loss is zero during calibration.
Adiabatic effect
The adiabatic effect can affect the accuracy of pressure gauge calibration when the pressure changes rapidly. As the pressure changes rapidly, the temperature of the fluid inside the gauge changes and this affects the density of the fluid, which in turn affects the pressure. This can cause errors in the gauge's reading, which can lead to inaccurate calibration results.
To minimize the effects of the adiabatic effect during calibration, it is recommended to use a pressure gauge with a high-frequency response. Such gauges have a faster response time and can accurately measure pressure changes that occur rapidly.
Mounting position
The mechanical nature of the pressure gauge means that the position of the gauge can affect the pressure reading in the system. Thus, it is recommended that the gauge be calibrated in the same position as it is used in the actual process for pressure measurement. The manufacturer’s guide should also be strongly referenced to ensure accurate mounting.
Pressurizing or exercising the gauge
Movement in mechanical pressure gauges causes friction. Exercising or pressurizing before calibration can reduce friction. Do this by supplying the nominal pressure, maintaining it for a minute, and then relieving it. Repeat this two or three times.
Readability
During calibration, adjust the input pressure so that the indicator needle always lands on a major scale mark instead of in between them. This makes the calibration process more convenient.
Hysteresis
Hysteresis in pressure gauge calibration refers to the difference in pressure readings when a gauge is subjected to increasing and decreasing pressure. In other words, it is the difference in the pressure reading when a gauge is calibrated while increasing the pressure, compared to the reading when it is calibrated while decreasing the pressure. This difference can be caused by various factors such as mechanical wear, temperature changes, and gauge design. It is important to take hysteresis into account when calibrating pressure gauges to ensure accurate measurements.
Repeatability
One of the qualities of an accurate pressure gauge is its repeatability, or the ability to produce the same reading for the same input. If the gauge is providing different results each time, it needs calibration. It is recommended to pressurize the gauge for 3 cycles before calibration.
Environmental condition
The reading in the gauge may vary depending on the different temperatures the process may be exposed to. The pressure gauge is usually calibrated at normal room temperature; hence the temperature change can reflect on the accuracy of the pressure reading. Thus, it is recommended to record the temperature and humidity when calibration is performed.
Metrological traceability
Metrological traceability is important in pressure gauge calibration, as it ensures that the pressure readings produced by the gauge are accurate and consistent with the international system of units (SI). To achieve metrological traceability in pressure gauge calibration, the gauge must be calibrated against a standard that is itself traceable to the SI. This is usually done by comparing the gauge to a known standard, such as a deadweight tester or a primary pressure standard.
Calibration uncertainty
The uncertainty in calibration can indicate the possible difference in the calibrated value. This uncertainty can be sourced by environmental conditions, reference devices, or operators taking the reading. It is important to be aware of the calibration uncertainty and be able to distinguish error from uncertainty. TUR (Test Uncertainty Ratio) or TAR (Test Accuracy Ratio) calculators are one of the ways to be aware of related uncertainty, although not all related uncertainties are covered. Therefore, it is recommended to calculate the total uncertainty of the calibration to identify how good the calibration is.
Calibration intervals
To ensure accuracy of the reading, pressure gauges require regular calibration. However, the calibration needs may vary depending on the usage and design of the gauge. Although there is no a fixed answer, a common recommendation is once a year. But it is also necessary to check for the manufacturer’s recommendation on the calibration period. Pressure gauges used in harsh operating conditions may require more frequent calibration.
In-house vs outsourcing calibration
For efficient pressure gauge calibration, it can either be done in-house or outsourced. The best choice may come down to the resources that a company is willing to invest.
In-house calibration requires the company to invest in calibration equipment, technicians, training, and creating a controlled environment. However, even with these provisions, it is difficult to obtain proof of the accuracy of the calibration. This is because gauges and calibration equipment needs to consistently meet all the strict national and international standards to be able to certify the calibration process which can be tough for small in-house facilities. Such standards include:
- ISO/IEC 17025: This standard allows laboratories to demonstrate that they operate competently and generate valid results, therefore promoting confidence in their work locally and internationally.
- ASME B40 - 2013: This standard from the American Association of Mechanical Engineers comprises various standards for pressure gauges, elements, diaphragm seals, digital pressure gauges, and more. The manual provides information on terminology and definitions, dimensions, safety, construction, and installation issues, as well as testing and calibration procedures and general recommendations.
Read our technical articles to learn more about how pressure gauges work, pressure gauge maintenance and selection criteria.
FAQs
Should pressure gauges be calibrated?
Yes, they should be calibrated to ensure process safety and efficiency.
How often should a pressure gauge be calibrated?
Calibrate a pressure gauge at least once a year.