What Is a Pneumatic Stopper Cylinder?
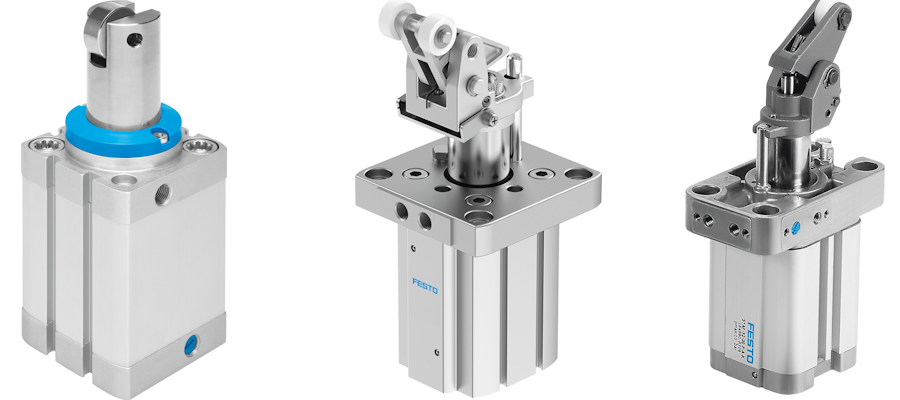
Figure 1: Festo pneumatic stopper cylinder: DFSP (left), DFST-G2 (middle), and STAF (right)
A pneumatic stopper cylinder regulates movement and halts workpieces or carriers at specific points on conveyor systems or assembly lines. These cylinders are vital components in modern transport systems, ensuring the smooth and safe operation of assembly lines by effectively stopping moving parts. This article discusses the key features, selection criteria, and applications of Festo pneumatic stopper cylinders.
Table of contents
- Pneumatic stopper cylinder working principle
- Selecting the right stopper cylinder for an application
- Pneumatic stopper cylinder DFSP
- Pneumatic stopper cylinder DFST-G2
- Pneumatic stopper cylinder STAF
- Stopper cylinders vs feed separators
Pneumatic stopper cylinder working principle
Pneumatic stopper cylinders can be either single-acting or double-acting, depending on their design.
Single-acting with spring return
This is the most common type for stopper applications.
- Initial state: The piston rod is extended due to an internal spring, positioning the stopper (roller or foot) in the "up" position, allowing objects on the conveyor to pass freely. No air pressure is applied at this point.
- Stopping a conveyor item: When a box or pallet needs to be stopped, compressed air is directed to the single port of the cylinder. This air pushes against the piston inside the cylinder.
- Stopping action: The compressed air overcomes the spring force and retracts the piston rod, bringing the stopper (roller or foot) down to make contact with the conveyor and stop the item.
- Resetting: Once the item is stopped and secured, the air supply is shut off. The internal spring then pushes the piston back to its original position, raising the stopper and allowing objects to flow again.
Double-acting
Double-acting cylinders offer more control as they have air ports for both extending and retracting the piston rod. There are two main configurations:
1. Double-acting with spring: Similar to the single-acting version, a spring provides a default position. Compressed air can be applied to either port:
- Air to the 'extend' port pushes the piston rod out, raising the stopper.
- Air to the 'retract' port overcomes the spring and pushes the piston rod in, lowering the stopper.
2. Double-acting without spring: This version relies solely on compressed air for both extension and retraction. Air is applied to the desired port to move the piston rod and position the stopper.
In both single-acting and double-acting versions with a spring, the spring dictates the default position, and compressed air is used to overcome the spring and move the piston in the opposite direction. The backward movement of the stopper (when compressed air pushes the piston) doesn't directly control the air input. It's a mechanical consequence of the air pressure overcoming the spring. Once the air supply is shut off, the spring takes over and returns the piston to its original position.
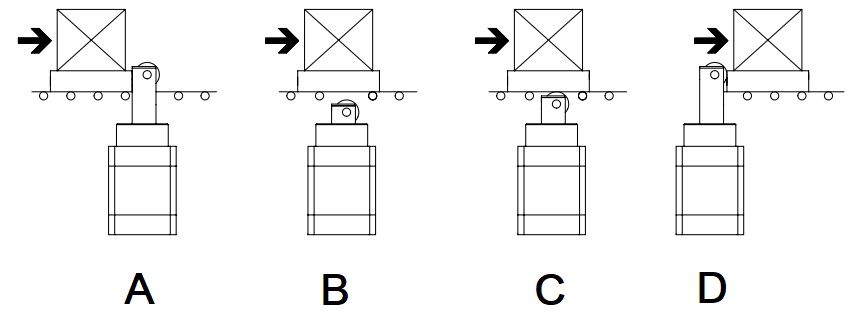
Figure 2: Festo roller pneumatic cylinder working: Sudden stopping of the conveyed goods by the piston rod (A), the conveyed goods are released by actuating the cylinder (B), the cylinder is then pushed forward by spring force until the roller touches the conveyed goods, allowing them to continue moving forward (C), after the conveyed goods have passed, the cylinder moves to its end position, ready to stop the next set of conveyed goods (D)
Selecting the right stopper cylinder for an application
There are three Festo stopper cylinder models to choose from - DFSP, DFST-G2, and STAF:
-
Load requirements:
- DFSP: Best for light loads up to 90kg.
- DFST-G2: Offers a wider range, handling 40kg (size 32) to 800kg (sizes 50-80).
- STAF: Suitable for stopping loads up to 150kg.
-
Application needs:
- DFSP: Ideal for conveyors where compactness, long service life, and easy setup are crucial.
- DFST-G2: Prioritizes gentle stopping with adjustable shock absorbers and quiet operation.
- STAF: Focuses on fast and simple conveyor line setup with a spring return safety feature.
-
Position sensing:
- DFSP: Offers sensor slots on three sides for flexible integration of proximity switches.
- DFST-G2: Provides versatile sensing for both toggle lever and piston positions.
- STAF: Includes integrated proximity switches for space-saving design.
Additional considerations
- All three cylinders operate with a pressure range of 1 to 10 bar.
- DFSP offers the widest ambient temperature range (-10°C to +80°C) compared to DFST-G2 (5°C to 60°C) and STAF (0°C to +60°C).
- Mounting options vary:
- DFSP: Most versatile, with direct mounting, flange mounting, through-hole mounting, and end cap mounting options
- DFST-G2: Uses through-hole mounting with a guide rod
- STAF: Employs flange mounting
Pneumatic stopper cylinder DFSP
Key features
- Compact design: Allows for easy integration into various systems without requiring significant space.
- Sensor slots on three sides: Facilitates the easy installation of position sensors for accurate control.
- Long service life: Achieved through excellent cushioning characteristics and a sturdy piston rod guide.
- Safe stopping: Capable of safely stopping workpiece carriers, pallets, and packages weighing up to 90 kg.
Types and versions
Trunnion:
- Available in single-acting, double-acting with spring, and double-acting without spring models.
- Models with protection against rotation are crucial for applications requiring precise alignment.
- Trunnion mounts provide a pivot point for the cylinder, allowing it to swing in a limited arc.
- Trunnion with female thread: Similar to the standard trunnion version but with the addition of a female thread for enhanced compatibility with various attachments and fittings.
Roller:
- Typically available in double-acting configurations, with or without spring assistance.
- Inherently includes protection against rotation due to its design.
- Easily integrated into conveyor systems, minimizing friction and resistance.
Selection criteria
1. Load capacity: Ensure the chosen model can handle the maximum weight of the conveyed goods (up to 90 kg).
2. Actuation type:
- Single-acting: Choose if force is only needed in one direction and air supply is limited.
- Double-acting with spring: Opt for applications requiring force in both directions with added spring assistance for return.
- Double-acting without spring: Suitable for applications needing forceful extension and retraction without the need for a spring.
3. Protection against rotation: Select a model with protection against rotation if maintaining the orientation of the stopped object is critical.
4. Mounting options:
- Direct mounting: Consider if the cylinder will be directly mounted to a surface or component.
- Through-hole mounting: Opt for this if the cylinder needs to be secured through a panel or bracket.
- Mounting flexibility: Trunnion mounts offer more flexibility in alignment and positioning.
Applications
-
Trunnion versions:
- Commonly used in automated manufacturing lines, packaging systems, and assembly processes where precise positioning and stopping of heavy loads are required.
- The trunnion mount's flexibility makes it suitable for applications where alignment may vary.
-
Roller version:
- Ideal for conveyor systems handling packages, pallets, or workpiece carriers, especially in distribution centers, warehouses, and production facilities.
- The roller design minimizes wear and facilitates smooth interaction with moving loads.
Pneumatic stopper cylinder DFST-G2
Key features
- Gentle and quiet operation: Features a cushioned toggle lever mechanism that ensures workpieces are stopped gently, minimizing vibrations and noise.
- Adjustable working direction: Offers versatility with an adjustable active direction due to the rotatable toggle lever setup that can be positioned at 90°, 180°, or 270°.
- High impact load capacity: Designed to handle impact loads of up to 800 kg, making it suitable for a wide range of industrial applications.
- Integrated, adjustable shock absorber: Ensures smooth and adapted stopping of workpieces, enhancing process reliability and product safety.
- Position sensing capability: Allows for position sensing on the piston, enabling precise control and monitoring of the stopping process.
- Lever locking mechanism: Provides the option to lock the toggle lever in place, ensuring workpieces remain securely stopped as needed.
- Toggle lever deactivator: Offers the ability to temporarily deactivate the toggle lever, allowing for the uninterrupted passage of items when required.
- Material options for rollers: Available with rollers made of polyamide for quieter operation or steel for increased durability and load capacity.
Selection criteria
1. Load capacity: Ensure the chosen model can handle the maximum weight of the workpieces (up to 800 kg).
2. Adjustable working direction: Choose a model that allows for the required toggle lever positioning (90°, 180°, or 270°) to fit the system's layout.
3. Shock absorption: Select a model with an adjustable shock absorber to ensure smooth stopping and minimize impact on delicate loads.
4. Lever mechanisms:
- Lever locking mechanism: Choose this feature if precise positioning and secure stopping are critical.
- Toggle lever deactivator: Choose this feature for applications requiring the temporary passage of items without stopping.
5. Roller material:
- Polyamide rollers: Suitable for environments where noise reduction is a priority.
- Steel rollers: Ideal for heavy-duty applications with higher load requirements.
Applications
- General industrial use: Suitable for a wide range of industrial applications, including those requiring high impact load capacity and precise control.
- Automated manufacturing lines: Ideal for stopping workpieces gently and quietly, minimizing vibrations and noise.
- Packaging systems: Ensures smooth and reliable stopping of packages, enhancing process reliability.
- Assembly processes: Provides precise control and monitoring of the stopping process, essential for high-precision assembly tasks.
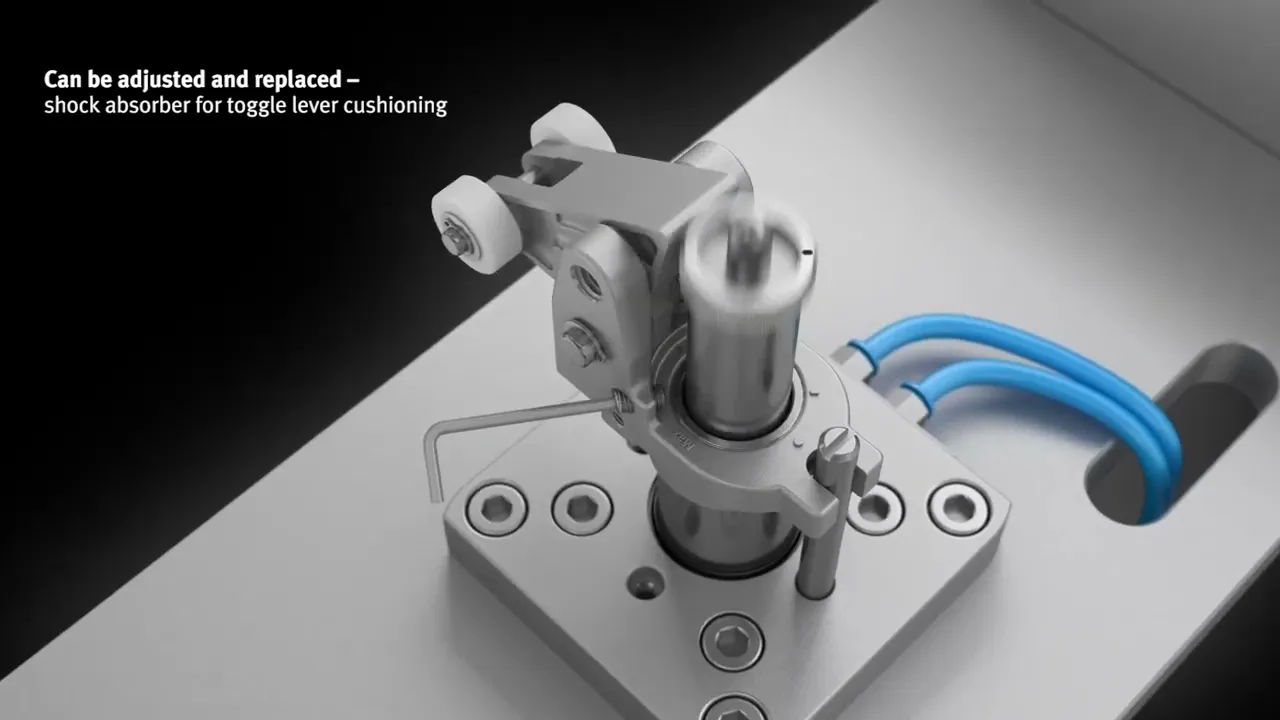
Pneumatic stopper cylinder STAF
Key features
- Single-acting vs double-acting: Offers both single-acting cylinders, ideal for simpler applications with a spring return mechanism, and double-acting cylinders, suited for more demanding tasks requiring controlled movement in both directions.
- Fast and simple setup: Designed for easy integration into conveyor lines, ensuring minimal downtime and straightforward maintenance.
- Load capacity: Capable of safely stopping loads up to 150 kg.
- Actuation: Simple actuation via a valve terminal, with flange-mounted solenoid valves enabling fast response times.
- Space-saving design: Integrated proximity switches for sensing saved space and simplify installation by eliminating the need for external sensors.
- Safety features: A spring return mechanism ensures the piston rod retracts safely in case of pressure loss, adding an essential layer of safety to operations.
Selection criteria
1. Load capacity: Ensure the chosen model can handle the maximum weight of the workpiece carriers or pallets (up to 150 kg).
2. Actuation type:
- Single-acting: Choose if force is only needed in one direction and a spring return mechanism is preferred for safety.
- Double-acting: Choose for applications requiring controlled movement in both directions.
3. Operating pressure: Select a cylinder that operates within the system's pressure range (1 to 10 bar) for optimal performance.
4. Mounting options: Flange mounting ensures stable and secure installation, ideal for dynamic industrial settings.
5. Position sensing: Integrated proximity switches for precise position detection, enhancing control and automation capabilities.
Applications
- Conveyor systems: Commonly used in industrial settings for stopping or separating pallets on conveyor systems.
- Automated assembly lines: Ideal for managing the flow of materials, ensuring precise control and timing of operations.
- Packaging stations: Ensures smooth and reliable stopping of packages, enhancing process reliability.
- Material handling systems: Provides robust and reliable stopping of workpiece carriers, essential for efficient material handling.
Stopper cylinders vs feed separators
Stopper cylinders are pneumatic devices designed to halt or control the movement of workpieces or carriers on transport systems. Their primary function is to interrupt or block the progress of moving parts for operational purposes, such as during assembly line processes. The cushioning feature allows for the gentle stopping of heavy loads, minimizing impact and vibration.
Feed separators, on the other hand, are specialized in separating individual workpieces from a continuous flow, such as those coming from a spiral conveyor or a conveyor belt, and directing them to subsequent processing stations. These devices are adaptable, with mounting options for various attachments to tailor the separation process to specific needs.