Pneumatic Drill - How It works
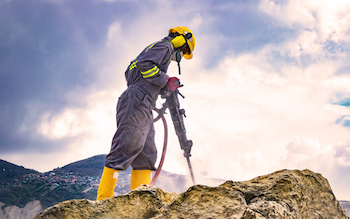
Figure 1: Pneumatic drill in construction site
A pneumatic drill is a handheld air-powered tool that drills holes or destroys hard surfaces such as rock, concrete, and roads. It is commonly referred to as a jackhammer or air drill. A pneumatic drill can drill holes about 10-20 mm in diameter and is applicable in rescue operations and construction. This article explores the working principle of a pneumatic drill and its comparison with electric drills.
Table of contents
- What is a pneumatic drill
- Pneumatic drill components
- How does a pneumatic drill work?
- Safety precautions when using pneumatic drills
- Noise from pneumatic drills
- Pneumatic vs electric drills
- FAQs
View our online selection of air hammers & chisels!
What is a pneumatic drill
A pneumatic drill relies on compressed air pressure for power. Pneumatic drills are one of the most efficient drilling tools in the market in terms of capacity, productivity, and functionality. For example, a sledgehammer will hit the ground ten times a minute, while pneumatic drills can hit the ground 1500 times every minute. This efficiency level makes pneumatic drills the tool of choice when drilling holes in hard surfaces or breaking large things. DIY projects, especially during house remodels and renovations, use pneumatic drills. Pneumatic drills fall under ISO 11148-3:2012. ISO 11148-3:2012 applies to power tools (non-electric) that are considered for rotary hole drilling in materials like metal, wood, plastics, and concrete, or for tapping and cleaning threads in plastics and metals. The standard applies to drills (normal or heavy-duty) with two handles and tappers, and does not apply to special requirements and modifications of drills and tappers for the purpose of mounting them in fixtures.
Pneumatic drill components
A pneumatic drill consists of a handle and an outer casing. Inside the drill are a valve, a pile driver, and a network of tubes. The drill bit protrudes outside the case and extends when the drill operates. In addition, the pneumatic drill connects to a diesel-powered air compressor via a thick air hose. The drill bit can is changeable to accommodate differently shaped drill bits (such as wide or narrow chisels) for different functions. The air compressor looks like an electric generator and is usually on wheels.
How does a pneumatic drill work?
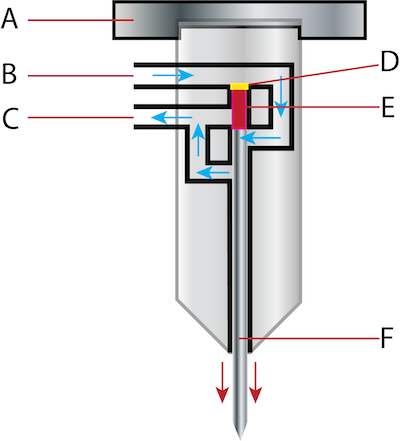
Figure 2: Pneumatic drill action when the user presses the handle: handle (A), air inlet (B), air out (C), valve (D), pile driver (E), and drill bit (F).
When the operator presses down the handle (Figure 2 labeled A), the compressor pumps air into the pneumatic drill through a spring-loaded valve on one side (Figure 2 labeled B). The pneumatic drill encloses a circuit of air tubes, a heavy piledriver (Figure 2 labeled E), and a drill bit towards the bottom (Figure 2 labeled F). First, the high-pressure air flows one way around the circuit. This forces the piledriver down, so it pounds into the drill bit, smashing it into the ground.
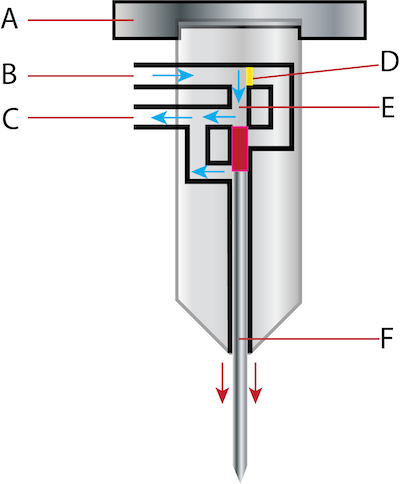
Figure 3: Pneumatic drill showing the valve flipping and change of air circulation: handle (A), air inlet (B), air out (C), valve (D), pile driver (E), and drill bit (F).
Then, a valve inside the tube network flips over, causing the air to circulate in a different direction (Figure 3). The piledriver moves back upward at this point, making the drill bit rise from the ground. The valve flips over again after a short while, and the process repeats. The piledriver smashes down on the drill bit around twenty-five times per second, so the pneumatic drill pounds up and down on the ground 1500 times per minute.
Safety precautions when using pneumatic drills
Pneumatic drills are heavy machinery requiring great strength and safety precautions. The drill hitting the ground produces rough vibrations, which pose a risk for the operator. These vibrations can cause the operator to experience poor circulation in their hands and wrists and, in time, develop carpal tunnel syndrome. To prevent this, operators should take breaks between drilling. Operators should also wear the usual shatter-resistant glasses and protective clothing.
Noise from pneumatic drills
Pneumatic drills are noisy, but there are newer versions with reduced noise. For example, some newer pneumatic drills feature a silencer around the tool's barrel. Even with such silencers, sounds from the compressor engine and the loud air exhaust are still major noise concerns. In fact, noise levels from a pneumatic drill can reach 120 dB, depending on the brand and surface. For this reason, all operators should wear hearing protection when operating pneumatic drills. If operators fail to wear ear protection, they can develop hearing loss and major tinnitus symptoms.
Pneumatic vs electric drills
Electric drills, also known as electric jackhammers, operate similarly to pneumatic drills. However, an electric power source and electric motor powers electric drills. The electric drill does not rely on a diesel-powered air compressor. The drill features a motor that rotates the crack, also known as a cam, and then converts the rotor motion into a back-and-forth or up-and-down motion to pump a piston. This piston powers a second piston, which then powers the shaft connected to the chisel. Electric drills are not as powerful as pneumatic drills.
When to use pneumatic drills
- During large construction, excavation, mining, and tunneling projects
- On hard surfaces such as concrete and asphalt
- Projects that will take a significant amount of time to achieve
When to use electric drills
- Short-term projects and more straightforward projects, such as home remodeling and renovations
- Working with less complicated surfaces such as bare ground and hardwoods, etc.
Pros and cons of pneumatic drills
Like any other air power tool, pneumatic drills have pros and cons.
Pros
- Simple operation: Pneumatic tools are generally easier to operate as they do not rely on intricate processes.
- Does not need electricity: Because they are diesel-powered, pneumatic drills can be used even in remote areas without electricity.
- Powerful: The pneumatic drill produces more torque than the electric drill and is, therefore, suitable for large and complex construction and mining projects.
- Lighter: Generally, the pneumatic tool is lighter than the electric tool and simpler to use.
Cons
- Noise: Vibrations caused by the drill can reach 100-120 dB, and the air compressor also creates an overall noisy environment.
- Storage space: Because of the diesel-powered air compressor, the complete set of a pneumatic drill needs larger storage than an electric drill needs.
- Expensive upfront: The initial investment of pneumatic drills is higher, but this drill is cheaper and more convenient in the long term.
FAQs
What does a pneumatic drill do?
Pneumatic drills find applications in drilling small halls on hard surfaces, such as asphalt. These drills are common in construction, mining, and home remodeling.
What is the noise level of pneumatic drills?
Pneumatic drills are quite noisy and can reach 120 dB from 2 meters away.
What are the components of a pneumatic drill?
A pneumatic drill consists of the diesel-powered air compressor, the outer casing, the handle, and the air inlet, and outlet valve. Inside the casing are tubes, a diaphragm valve, and the pile driver.
How does a pneumatic drill work?
Compressed air powers the pneumatic drill, which moves the pile driver up and down, causing the drill bit to impact the drilled surface.