Maintenance and Care For Industrial Coolant Hoses
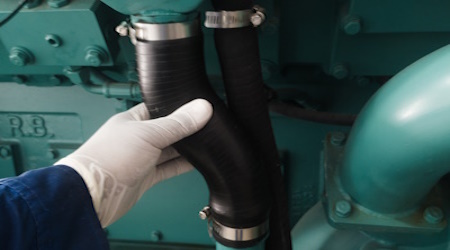
Figure 1: Inspecting coolant hose
Properly maintaining industrial coolant hoses is critical to ensure efficient operation, prevent downtime, and avoid costly equipment damage. They are flexible tubes that transport coolant to prevent machines and components from overheating in a wide range of applications. This article highlights the importance of routine inspection, timely replacement, and correct handling of industrial coolant hoses to maintain their functionality and prolong the service life of the associated equipment.
View our online selection of hoses!
What is an industrial machine coolant hose
An industrial coolant hose is a flexible tube that transports coolant to and from industrial machinery. Coolant is a fluid that absorbs and transfers heat away from machinery, preventing it from overheating. For example, coolant hoses are used with machine tools, such as CNC mills and lathes, to prevent the tools from overheating and damaging the workpiece. Also, they transport coolant between the engine and radiator to keep the engine from overheating. Industrial coolant hoses are typically rubber or plastic designed to withstand high temperatures, pressures, and chemical exposure. They are specifically designed to withstand high temperatures, pressures, and chemical exposure and are often constructed with multiple layers of reinforcement to improve their strength and durability.
Read our flat hose overview article for more details on the structure and application of flat hoses in industries.
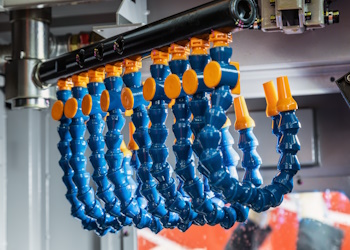
Figure 2: Coolant hose on machinery
Maintenance
Consider a semiconductor manufacturing industry where precise temperature control is crucial. A coolant hose failure could lead to overheating, causing damage to sensitive electronic components or wafers during production, potentially resulting in costly scrap and downtime for maintenance and calibration of affected equipment. It is advised to check coolant hoses regularly and replace them if needed. There are a few steps to prevent coolant hose leaks and failures:
- Regularly inspect coolant hoses for signs of wear and tear. This includes looking for cracks, fraying, bulges, and other damage. Replace any damaged hoses immediately.
- Test coolant regularly for pH, concentration, and contamination. Replace the coolant according to the manufacturer's recommendations.
- Clean coolant hoses periodically to remove dirt, debris, and coolant residue.
- Ensure that coolant hoses are properly routed and not kinked or pinched. Kinking and pinching can restrict the flow of coolant and damage the hose.
- Tighten hose clamps periodically to prevent leaks.
Coolant hose repair and replacement
Check for the following signs that indicate a defective coolant hose:
- Visible damages: Visible damage such as holes, cracks, or swelling, as well as a spongy feel when pressing the hose, are clear indications of internal deterioration and necessitate hose replacement.
- Leaks: Leaks are serious issues caused by factors like cracks, loose hose clamps, and corrosion; they can lead to engine overheating and costly repairs. If the leak is small and the coolant hose is in good condition, try tightening the clamps or using a repair tape or sealant. However, if the leak is large or the hose is damaged, it is best to replace it.
- Collapse: Coolant hose collapse, often resulting from high heat, pressure, or vacuum, indicates that its reinforcement has failed and cannot maintain its shape, requiring immediate replacement.
- Failure: Coolant hose failure can stem from age, wear and tear, and exposure to extreme temperatures; regular inspection and replacement of hoses is crucial to prevent this.
- Cracks: When squeezing the hose, any cracks in the outer layer may signal a risk of future rupture. The hose should be flexible and supple without bulges or swelling, which could indicate oil exposure or internal failure. Areas of chafing, where the textile reinforcement is exposed due to constant wear from hot or abrasive components, also call for hose replacement.
In short, replace the hose if it turns brittle or hard, cracks, bulges, or shows signs of abrasion.
How to replace a coolant hose
Before starting, ensure that the machinery is turned off, the engine is cool, and all safety protocols are followed. Wear appropriate personal protective equipment (PPE).
- Drain the coolant: Drain the coolant from the system into a suitable container for proper disposal or reuse.
- Remove old hose: Loosen the clamps or fittings that secure the hose to the machinery. Carefully remove the hose, taking care not to damage surrounding components.
- Inspect and clean: Inspect the fittings and connections for corrosion or damage. Clean the area where the hose attaches to ensure a good seal with the new hose.
- Install the new hose: Position the new hose correctly and secure it with clamps or fittings. Ensure it's not twisted or kinked, which can restrict coolant flow.
- Refill with coolant: Refill the system once the new hose is installed. Follow the manufacturer's specifications for the type and amount of coolant.
- Bleed the system: Remove any trapped air by bleeding it according to the manufacturer's instructions. This often involves running the engine and opening bleed valves.
- Check for leaks: After the coolant has been added and the air has been bled from the system, check for leaks around the hose connections.
- Test: Start the machinery and let it reach operating temperature. Monitor the temperature and check for leaks again.
- Documentation: Record the maintenance activity, including the date of replacement and any observations, in the machinery's service log.
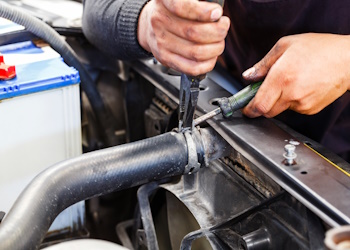
Figure 3: Repairing coolant hose
Read our hose selection criteria for more details on how to select a hose for an application.
FAQs
How to deal with coolant leak from hose?
Promptly identify the leak source and either apply a temporary fix using repair tape or sealant or get a proper replacement of the damaged hose.
Can you temporarily fix a hose leaking coolant?
A temporary fix for a leaking coolant hose might involve using a patch kit or sealant, but it's only a short-term solution; the hose may need to be replaced soon.
How to fix a coolant hose leak?
To fix a coolant hose leak, identify the source of the leak, drain the coolant system, remove the damaged hose, install a new hose with the correct specifications, and refill the coolant system.