Sanitary Pressure Gauge
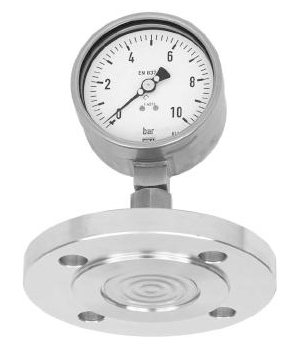
Figure 1: A diaphragm pressure gauge with stainless steel casing for hygienic applications.
A hygienic pressure gauge is necessary for environments where hygiene is a primary concern, such as in the pharmaceutical, biotechnology, and food and beverage industries. These gauges typically have a non-porous housing to prevent the growth of bacteria or other microorganisms. They may also have features such as easy-to-clean surfaces and sealed-for-life construction. They are commonly referred to as sanitary pressure gauges.
Hygienic pressure gauges utilize a diaphragm mechanism to measure pressure. For most hygienic applications, standard diaphragm pressure gauges are adequate. However, high-end diaphragm pressure gauges are available for applications requiring strict adherence to specific standards or additional safety measures. This article explicitly covers high-end diaphragm pressure gauges for hygienic (sanitary) applications. Also, read our article on standard pressure gauges to understand the basics of a pressure gauge.
Table of contents
View our online selection of pressure gauges!
Flush welded diaphragm
Diaphragm elements are circular-shaped, corrugated membranes either clamped around their rim between two flanges or welded. The pressure of the media acts on one side of the diaphragm. This causes a deflection in the membrane, amplified by gears and linked to the pointer on the gauge to indicate the pressure. Read our article on diaphragm pressure gauges for more information on the construction and selection criteria of diaphragm pressure gauges.
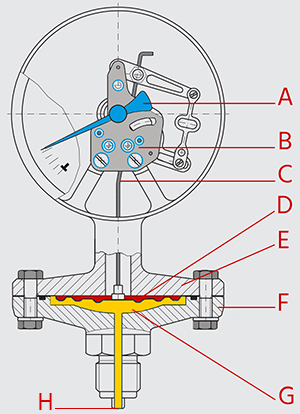
Figure 2: Diaphragm pressure gauge operating principle: pointer (A), movement (B), link (C), diaphragm (D), upper housing (E), lower housing (F), pressure chamber (G), and pressure entry point (H).
A diaphragm seal is a barrier between the pressure measurement instruments and potentially harmful media, such as corrosive substances or debris that may cause clogging. However, at times even diaphragm seals are not entirely immune to clogging, leading to equipment malfunction and disrupting the process. To combat this issue, a flushing connection can be utilized. This is a supplementary connection integrated into the lower housing of the diaphragm seal, allowing operators to flush debris from the diaphragm's surface and prevent clogging. The diaphragm seal types can be either threaded or flanged when they come with a flushing connection.
When not in operation, a flushing plug or valve should be used to seal off the flushing connection and prevent the process media from leaking out. It is important to verify that the flushing plug is constructed from the same material as the lower housing to ensure compatibility with the process. Additionally, ensure that the internal components of the valve that interact with the media are suitable for the particular type of media being used. Read our article on chemical compatibility for more details.
Advantages
Flush welded diaphragm pressure gauges offer several advantages over standard pressure gauges.
- Flush-welded diaphragms measure dry. This means that the diaphragm separates the liquid or gas being measured from the pressure-sensing parts of the pressure gauge. This protects both the pressure gauge and the system liquids or gasses from contamination. Also, in a hygienic pressure gauge, this diaphragm is typically two to five times thicker than a conventional seal diaphragm.
- Flush-welded diaphragm pressure gauges provide continuous and reliable measurement, even in critical operations, due to the robustness of the diaphragm element and high overload safety. In comparison to standard pressure gauges, hygienic gauges are less susceptible to unexpected process conditions (pressure peaks, overload) and mechanical influences.
Contamination
Contamination of process fluids or gasses can have severe consequences, like material and financial losses for the pharmaceutical, biotechnology, and food and beverage industries. A single foreign particle can alter the intended dosage of a product. Therefore, it is essential for pressure gauges used in these processes to comply with strict sanitary standards and measures that counter contamination at all levels. Hygienic pressure gauges employ various methods to ensure the prevention of contamination in the media.
- Using flush diaphragm element pressure gauges
- Secondary safety devices: Some hygienic pressure gauges have been fitted with secondary safety devices, such as a second protective barrier and a monitoring element for the diaphragm. In the event that the diaphragm breaks, these safety devices ensure that the process media and measuring instruments remain separated from each other, preventing the medium from escaping into the environment and preventing any contaminants from entering the process.
Sanitation
Hygienic pressure gauges are designed with several approvals and compliances. The approvals necessary for a particular hygienic pressure gauge depend on the intended industry (like pharmaceutical or food). Cleanliness is a critical feature of sanitary gauges.
- EHEDG compliance: EHEDG is an industry consortium representing equipment manufacturers, food manufacturers, research institutions, and public health authorities. It was founded in 1989 to promote hygiene during the processing and packaging of food.
- CIP/SIP cleaning: In many industries that require frequent cleaning or sterilization of equipment, such as pharmaceuticals and food & beverage, integrated clean-in-place (CIP) and sterilize-in-place (SIP) solutions play a pivotal role.
- Autoclavable: Medical autoclaves are specialized devices that use high-pressure steam to eliminate bacteria, viruses, and other microorganisms from instruments and equipment. To determine if a pressure gauge is suitable for an autoclave, it must be labeled as ‘autoclavable,’ indicating that it has been designed and tested to withstand the high temperatures and pressures used in the sterilization process.
- FDA approval: The Food and Drug Administration (FDA) is a regulatory agency of the United States Department of Health and Human Services. Its primary responsibility is to protect public health by monitoring the safety and efficacy of food and pharmaceutical products.