Hydraulic Bottle Jacks
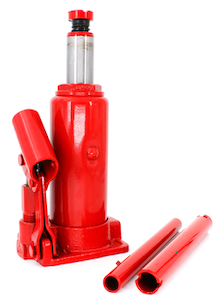
Figure 1: A hydraulic bottle jack lifts a steel beam.
Hydraulic bottle jacks are compact and simple-to-use tools that lift heavy loads. Due to their small size, these jacks fit nicely on a garage shelf or in a car trunk, making them versatile and readily available. Despite their small size, hydraulic bottle jacks can lift loads from 2 to 20 tons, and industrial bottle jacks can lift to 100 tons. This article focuses on how a hydraulic bottle jack's components and operation make it suitable for different applications. However, for a broader understanding of hydraulic jacks, read our hydraulic jack overview article.
Table of contents
- Hydraulic bottle jack design
- Hydraulic bottle jack working principle
- How to use a bottle jack
- Hydraulic bottle jack standards
- Hydraulic bottle jack applications
- FAQs
View our online selection of hydraulic jacks!
Hydraulic bottle jack design
A hydraulic bottle jack has several parts that work together to lift heavy loads.
- Bearing pad: The bearing pad (Figure 2 labeled A) makes contact with a lift point (e.g., lift points on a vehicle)
- Extension screw: The extension screw (Figure 2 labeled B) is adjustable to provide further lifting height.
- Hydraulic ram: The hydraulic ram (Figure 2 labeled F) rises from the bottle jack's body during operation.
- Filler plug: The filler plug (Figure 2 labeled C) is removable, allowing hydraulic oil refill.
- Handle: The handle (Figure 2 labeled D) has two pieces. Short handles work better in confined spaces, whereas longer handles provide greater leverage.
- Release valve: The release valve (Figure 2 labeled E) closes to allow for lifting and opens to allow for lowering.
- Socket: The up and down movement of the socket (Figure 2 labeled G) operates the pumping piston.
- Piston assembly: The piston assembly (Figure 2 labeled H) moves hydraulic fluid from the reservoir into the ram cylinder.
Note: Not all hydraulic bottle jacks have an overload valve. This valve releases pressure from the system if the jack is overloaded. At this point, the bottle jack’s ram will not continue to rise.
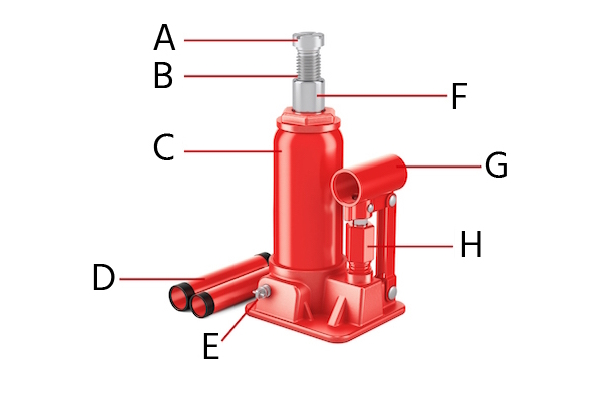
Figure 2: A hydraulic bottle jack’s components: bearing pad (A), extension screw (B), filler plug (not seen) (C), handle (D), release valve (E), hydraulic ram (F), socket (G), and piston assembly (H).
The exact minimum (fully lowered) and maximum (fully raised) heights of a hydraulic bottle jack depends on the manufacturer and lifting capacity. Typically, the higher the lifting capacity, the taller the bottle jack. For example, a 2-ton hydraulic bottle jack may have the following specifications:
- Minimum height: 148 mm (5.8 inches)
- Lifting height: 80 mm (3.1 inches)
- Adjustable height: 50 mm (2.0 inches)
- Maximum height: 278 mm (10.9 inches)
Hydraulic bottle jack working principle
A hydraulic bottle jack works according to Pascal's Law. According to Pascal's Law, pressure equals the quotient of force over area. In a bottle jack, moving oil from one cylinder to a larger one multiplies the force. This is how a user uses relatively little force to lift something heavy with a bottle jack.
When a bottle jack's handle (Figure 3 labeled E) moves up (Figure 3 center), the pumping piston (Figure 3 labeled F) siphons low-pressure fluid (Figure 3 labeled D) from the reservoir (Figure 3 labeled C). The reservoir check valve (Figure 3 labeled G top) opens, and the ram cylinder check valve (Figure 3 labeled G bottom) closes. This prevents the high-pressure fluid (Figure 3 labeled A) from the ram piston cylinder (Figure 3 labeled A) from flowing toward the pumping cylinder.
When the handle moves down (Figure 3 right), the reservoir check valve closes, and the ram cylinder's check valve opens. This controls the oil flow from the pumping piston to the ram cylinder and not back into the oil reservoir. Since the area of the ram cylinder is larger than the area of the pumping cylinder, force multiplies.
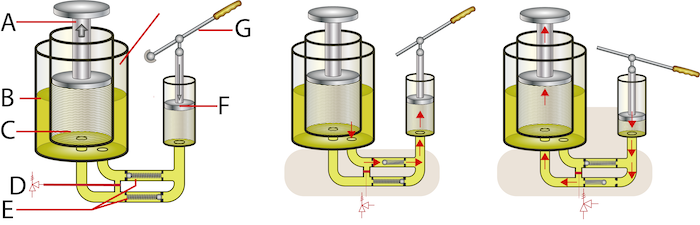
Figure 3: Hydraulic bottle jack working principle. Components (left): ram piston (A), low-pressure fluid (B), high-pressure fluid (C), pressure relief valve (D), check valves (E), oil reservoir (F), handle (G), and pumping piston (H). Lifting the handle (center) draws low-pressure fluid from the reservoir and pushing the handle down (right) pushes oil towards the ram cylinder.
How to use a bottle jack
Before using a hydraulic bottle jack, ensure that adequate jack stands are available and that what will be lifted is on a level surface. If lifting a vehicle, identify the lift points ahead of time by reading the vehicle's manual.
When ready to lift:
- Place the hydraulic bottle jack beneath the lift point.
- Adjust the extension screw, so the bearing pad is very close to the lift point.
- Ensure the release valve is closed.
- Use the handle to pump the jack and raise the hydraulic ram. Lift to the desired height.
- Place a jack stand next to the hydraulic bottle jack.
- Open the release valve to lower the load onto the jack stand and remove the jack from the work space.
After doing the necessary work:
- Close the release valve.
- Raise the hydraulic ram to take the load off the jack stand.
- Remove the jack stand.
- Slowly open the release valve to slowly lower the load until it is off the hydraulic bottle jack.
Hydraulic jack stands
It is not safe to hold the load on the hydraulic bottle jack during the completion of work. Therefore, a jack stand is necessary. Jack stands typically come in one of two materials: aluminum and steel.
- Aluminum: Aluminum jack stands have two major benefits: rust and corrosion resistance and light weight. Although aluminum does not rust, salt water will corrode it. If overloaded, the aluminum body will dent and deform.
- Steel: Given enough time, it is almost certain that a steel jack stand will rust. However, steel jack stands have the advantage of being able to hold much larger loads than aluminum jacks can. For heavy vehicles (e.g., trucks and tractors), steel jack stands are necessary.
Read our hydraulic jack maintenance and repair article for more details on how to maintain a hydraulic jack properly.
Hydraulic bottle jack standards
The ISO 11530 standard details design and safety requirements for hydraulic jacks that lift vehicles heavier than 3.5 tonnes. Hydraulic jacks that meet this standard are also applicable for smaller vehicles that have a lift point design specific for these jacks. Meeting this standard means that hydraulic jacks work efficiently and have a reduced chance of failure.
Hydraulic bottle jack applications
While it’s common to find a hydraulic bottle jack in a car repair shop, these jacks have uses in other industries:
- Construction: Bottle jacks can lift heavy loads such as steel beams or entire structures.
- Railroad: Hydraulic bottle jacks can lift or lower track rails for placement.
- Mining: Bottle jacks provide a safe method for lifting and moving heavy rocks.
- Agriculture: Hydraulic bottle jacks can lift heavy trailers and tractors to the proper height for working.
Read our floor jack article for more information on the working of hydraulic floor jacks.
FAQs
Can a bottle jack lift a truck?
A bottle jack with an appropriately high enough weight capacity can lift a truck.
How much weight can a hydraulic bottle jack lift?
Standard hydraulic bottle jacks can lift between 2 and 20 tonnes. Industrial bottle jacks can lift heavier loads.