Gate Valve vs Butterfly Valve
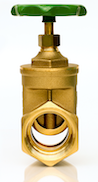
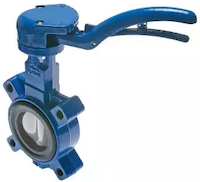
Figure 1: Gate valve (left) and butterfly valve (right)
At first glance, it is not simple to decide between a gate valve and a butterfly valve for an application. Therefore, it is important to understand the differences between these two valve types to avoid unnecessary setbacks in an operation. This article lays out the fundamental similarities and differences between a gate valve and a butterfly valve, which can be seen in Figure 1, and looks at their application suitability, advantages, and disadvantages.
Gate and butterfly valves are both used to turn on and off the flow, but butterfly valves can also regulate flow via partial disc closure. Butterfly valves are part of the quarter-turn family of valves and can be shut off much faster than gate valves, which are multi-turn valves. Gate valves are preferable for high-pressure systems whereas butterfly valves are preferable for larger port sizes. Learn more about the differences between quarter-turn and multi-turn valves in our article that compares lever handle valves to handwheel handle valves.
Table of contents
Gate valves
How does a gate valve work?
A gate valve is named after its disc, which behaves like a gate by either stopping or allowing media flow. It has a simple operation compared to other control valves, which makes it one of the most commonly used valves. Because a gate valve is a full-port valve, which means that the valve’s ports are the same size as the inner diameter of the connecting pipes, there is very little resistance to liquid or gas media that flows directly through it. Therefore, the pressure drop through the valve is quite low. For a more extensive understanding, read our article on gate valves.
Operating a gate valve
Gate valves are multi-turn valves, meaning the handwheel must turn more than 360° to fully open or close the valve. Turning the handwheel in one direction or the other moves the gate up or down via the stem. When the gate is completely up, the passageway is unobstructed, and media can flow. When the gate is down, media is blocked and cannot flow. Gate valves cannot modulate or throttle flow because there is a nonlinear relationship between the gate’s travel and flow rate. If the gate is partially open, the flow will crash into it while traveling through the valve, causing the flow to move at a higher velocity and create turbulence, both of which lead to increased wear on the disc and seats.
The three common means for actuating a gate valve are manually, pneumatically, or electrically. The manual method requires an on-site user to spin the handwheel to open or close the valve. This method is the most cost-effective since gate valves are not typically opened or closed often. The pneumatic and electric solutions allow for remote operation of a gate valve. Pneumatic actuation requires a pneumatic system on-site and electrical actuation requires electrical power on-site.
Gate valve types
As mentioned above, there exist different styles of gate valves. Three factors typically determine a gate valve's style: the gate type, the bonnet type, and the stem type.
Gate type refers to the disc that blocks the flow when the valve is closed, for example:
- Wedge disc: The gate is shaped like a wedge and it sits on two inclined seats. This provides a high wedging force which assists with sealing.
- Knife disc: The gate is a piece of metal with a beveled edge like a knife. It can be used to cut through thick fluids and dry solids.
- Double disc: The gate is two discs which sit on two seats. The discs expand away from each other to provide a tight seal.
Bonnet type refers to how the bonnet is attached to the valve body. It can be:
- Screwed: This is the simplest type of bonnet construction and is normally used in small size valves.
- Bolted: These bonnets are used in larger valves and high-pressure applications.
- Welded: The bonnet is threaded in and the body-bonnet joint is welded. This offers extra protection against leaking.
- Pressure sealed: The body-bonnet joint seal enhances as pressure within the valve increases. Used typically for high-pressure applications above 100 bar.
Stem type refers to the position and action of the stem
- Rising vs non-rising: Rising stem gate valves require more space above the valve than non-rising.
- Remains within the valve vs rises out of the valve upon opening: Rising out of the valve makes the stem easier to lubricate.
Materials
The correct material depends on the application's fluid service and temperature. Common materials used for a gate valve are:
- Body and bonnet: cast steel, stainless stell, cast iron, gunmetal, bronze, brass, and PVC
- Disc: stainless steel, polypropylene, Teflon, rubber lined (e.g., wedge disc)
- Seal: EPDM, NBR, Teflon
These materials allow for a range of applications, so gate valves apply to relatively mild applications like household plumbing to more corrosive applications such as use in saltwater environments. For more information, read our chemical resistance guide.
Butterfly valves
How does a butterfly valve work?
The essential operation of a butterfly valve is achieved by turning its handle 90° or using a pneumatic or electric actuator. This turns the valve's stem, which rotates the disc. In the fully closed position, the disc is perpendicular to the flow, and in the fully open position, the disc is parallel to the flow. Partial opening or closing of the disc can achieve proportional or throttled flow rates. In cases of a large butterfly valve or a valve used in a liquid application for which fast closure could produce water hammer, a butterfly valve can be gear operated via a gearbox (Figure 2, right). The gearbox’s handwheel must be turned more than 90°, though, which eliminates the butterfly valve’s relatively fast closing speed. For a more comprehensive understanding, read our article on butterfly valves.
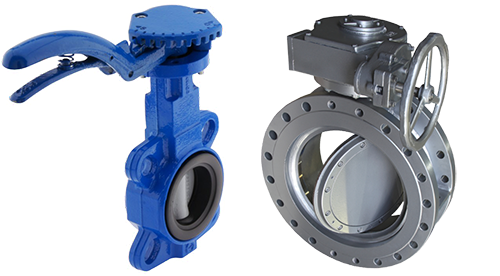
Figure 2: A zero offset butterfly valve with a lever handle on the left and an eccentric butterfly valve with a hand wheel on the right
Butterfly valve types
There are two key topics when discussing types of butterfly valves: body and stem offset. Body refers to how the valve's body connects with piping, and stem offset refers to whether the stem passes through the center of the disc or is offset.
The butterfly valve body types are:
- Double-flanged: This design is typically used for larger butterfly valves.
- Wafer: Most cost-effective design; sandwiched between two pipe flanges.
- Single flange: This design uses bolts and nuts passed through the valve’s holes to connect to both sides of the piping.
- Lug type: This design has threaded inserts, and bolts are used to connect pipe flanges to each side. Suitable for removing piping from one side without affecting the other.
- Flangeless: Like the wafer style, this design is sandwiched between two pipe flanges.
- Butt-welding ends: Prepared for welding directly to piping.
- U-section: Also clamped between pipe flanges and suitable for end-of-line service.
The stem can pass through the centerline of the disc (concentric) or be offset behind the centerline (eccentric). Offset, which can be single-, double-, or triple-offset, is used to reduce how much the disc rubs against the seating while closing. The higher the offset, the more the disc moves towards fully closed before contacting the seal. Any rubbing against the seal can reduce the service life of the valve. High-performance butterfly valves are specifically designed to withstand more demanding applications in terms of pressure and temperature.
The following compares a high-performance butterfly valve with a standard butterfly valve:
- Maximum shutoff pressure: Approximately 50 bar (725 psi) vs approximately 14 bar (203 psi)
- Tight shutoff: Below 260°C (500°F ) vs below 120°C (248°F)
- Shutoff with allowable seat leakage: Below 538°C (1000°F) vs below 425°C (797°F)
Read our article on butterfly valve design differences article for more details on the features of each design type.
Materials
The valve’s body and seat materials should be chosen carefully based on the needs of the application. Common body materials are iron, stainless steel, carbon steel, nickel alloy, titanium alloy, and nickel aluminum bronze. These materials vary in weight and resistance to corrosion and extreme temperatures.
Common seat materials are EPDM, EPDM white, FKM, XNBR, and NBR. Depending on the seat material, a butterfly valve can be used in temperatures ranging from -10°C to 180°C. Resilient and metal seated butterfly valves are also available, using the same materials listed here, and are designed to operate under more extreme temperatures and pressures.
Gate valves vs butterfly valves
There are many factors to consider when deciding whether a gate or butterfly valve is correct for a given application. Below are some of the most important:
- Cost: A butterfly valve is typically less expensive than a gate valve, especially at larger port diameters.
- Installation space: A butterfly valve takes up less installation space than a gate valve.
- Weight: A butterfly valve weighs less than a gate valve; the latter may need support structures at larger port diameters.
- Maintenance: While a butterfly valve is relatively easy to maintain, repair, or install due to its small size and low weight, its center disc makes it not suitable for systems that use pigging and swabbing for cleaning purposes. On the other hand, a gate valve is ideal for such maintenance.
- Operation: A butterfly valve can close faster than a similar port diameter gate valve. However, this fact means that butterfly valves are more susceptible to water hammer.
- Flow regulation: A butterfly valve can modulate or throttle flow, whereas a gate valve can only be on/off.
- Flow resistance: A gate valve offers less flow resistance and, therefore, less pressure drop than a butterfly valve.
- Pressure: Gate valves can handle higher pressures than butterfly valves.
Applications
- Gate valves have a higher sealing tightness, and therefore are more suitable for applications that require zero leakage.
- Butterfly valves are more suitable for applications that require flow modulation or throttling.
- If a slurry flow does not need to be modulated, gate valves are preferable to butterfly valves.
- Gate valves are more suitable for systems that require bi-directional, uninterrupted flow.
FAQs
Which is better, a gate valve or a butterfly valve?
A gate valve has a stronger seal and is more suitable for high-pressure applications. A butterfly valve is less expensive and available in very large sizes.
Can a butterfly valve be used instead of a gate valve?
A butterfly valve can be used instead of a gate valve in low-pressure systems for which some leakage is not a major concern.