Flare vs Compression Fittings
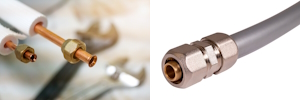
Figure 1: Flare (left) and compression (right) fittings are commonly used in piping systems.
Flare and compression fittings offer a reliable sealing mechanism, making them vital components in piping systems for various applications. This article compares flare and compression fittings, two commonly used fittings with distinct sealing methods and applications. Flare fittings are notable for their high-pressure resistance, while compression fittings offer easy assembly. Understanding their differences is key to selecting the appropriate fitting for any application.
When deciding between using a flare vs a compression fitting, consider the following:
- Pressure and temperature requirements: Flare fittings are better for high-pressure situations, while compression fittings are good for lower pressures.
- Installation and maintenance: Compression fittings are easier to put together and take apart, which is good for fixes or changes. Flare fittings take more work to install but might not need as much work later on.
- Connecting material: Flare fittings need tube material that is soft enough to be flared, such as copper.
View our online selection of hose and pipe connectors!
Designs
Flare and compression fittings have different general designs, but both use a nut to tighten the connection and provide a leak-proof fit.
Flare fittings
Flare fittings (Figure 2) involve flared tubing where the end of the pipe is expanded in a conical shape. The fitting has a matching conical surface and a nut over the tubing. When the nut is tightened, it presses the flared end of the tube against the fitting, ensuring a tight seal. This type of connection is valued for its high pressure and temperature resistance, making it suitable for gas and high-pressure applications.
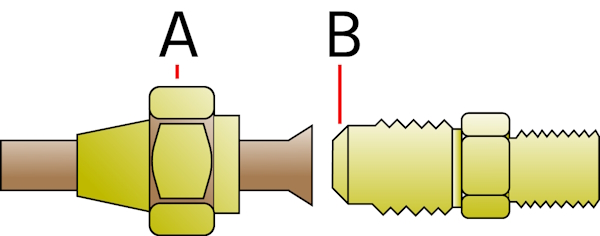
Figure 2: A flare fitting design: nut over the tube (A) and conical point (B) that fits into the tube's flared end.
Compression fittings
The components of a compression fitting are a nut, a ferrule or ring, and a body (Figure 3). The tube is inserted into the body of the fitting and held in place by the ferrule. As the nut is tightened, the ferrule compresses between the nut and the body, creating a seal. Compression fittings are appreciated for their ease of assembly and disassembly and are frequently used for water, gas, and hydraulic systems.
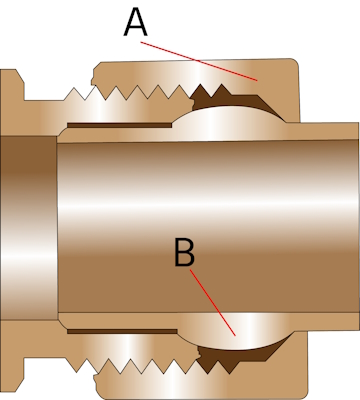
Figure 3: A compression fitting design: nut (A) and ferrule (B).
Applications
Flare fittings
Flare fittings are typically used in applications with high pressure, vibration, and thermal expansion/contraction. They provide a durable seal that can withstand these demanding conditions.
- High-pressure gas lines: Flare fittings, such as those for natural gas or propane, are often used in gas lines because they can handle high pressures without leaking.
- Refrigeration systems: The connections in refrigeration and HVAC systems often use flare fittings because they must withstand the pressure of refrigerants and the temperature changes without failing.
- Automotive brake lines: Flare fittings are used in automotive brake line applications because they create a secure, leak-free connection that can handle the high-pressure hydraulic fluid.
- Hydraulic systems: Heavy machinery and industrial hydraulic systems often utilize flare fittings to maintain a strong seal under the high-pressure conditions of hydraulic fluid transfer.
- Aerospace applications: The aerospace industry uses flare fittings for fuel, oil, and hydraulic lines because they can endure the extreme conditions of flight, which include rapid pressure and temperature changes.
Compression fittings
Compression fittings are often chosen for their ease of installation and maintenance. They are suitable for lower-pressure applications, and the system may require frequent disassembly and reassembly. For high-pressure applications, read our article on high-pressure compression fittings.
- Water plumbing systems: Compression fittings are commonly used in residential and commercial water plumbing systems for sinks, toilets, and other fixtures because they are easy to install and don't require special tools for connection.
- Instrumentation and control: Compression fittings allow for easy assembly and disassembly when adjustments or calibrations are needed in applications where precision measurement and control systems are used, such as in laboratories or manufacturing processes.
- Pneumatic systems: For systems that use compressed air, like pneumatic tools or air supply lines, compression fittings are often sufficient to provide a reliable seal at the typical working pressures involved.
- Low-pressure gas applications: For gas applications that operate at lower pressures, such as those in some household appliances or portable gas heaters, compression fittings can be suitable.
- Hot and cold water supply lines: Many hot and cold water supply lines to faucets, toilets, and appliances use compression fittings for their simplicity and ease of installation, especially in tight spaces where using a flare tool would be difficult.
Selection criteria
- Pressure and temperature: Flare fittings have metal-to-metal contact and offer a more reliable seal in high-pressure and high-temperature environments.
- Fluid type: Both compression fittings can be used for water, gas, and hydraulic systems. However, the fitting's compatibility with a specific fluid type must be verified to prevent leaks or material degradation.
- Ease of assembly: If a system requires frequent disassembly, compression fittings offer an advantage as they do not require special tools for assembly and can be easily disconnected and reconnected.
- Pipe or tube material: The material of the pipes or tubes is also important. Flare fittings typically require softer tubing materials that can be flared, such as copper or aluminum. Compression fittings are a suitable option if the tubing material cannot be flared.
FAQs
What is the advantage of flare fittings?
Flare fittings have a metal-to-metal connection, providing higher resistance to temperature and pressure.
How much pressure can flare fittings hold?
Depending on design, flare fittings can withstand up to 346 bar (5,000 psi).
Do compression or flare fittings require soldering?
No. Compression and flare fittings do not require soldering.