Flanged Valves vs Threaded Valves
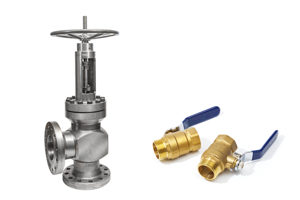
Figure 1: Flanged (left) and threaded valves (right)
Flanged and threaded valves are two commonly used types of valve fittings in industries. Choosing between them requires careful consideration of pressure, temperature, installation complexity, space constraints, and cost-effectiveness. This article explores and compares both valve types to help the user make an informed decision for an application.
Flanged valves
A flanged valve has flanges at the end of its body. A flange connection joins two materials with either an internal or external lip. A gasket placed between these materials stops leaks. Typically, bolts secure this connection; however, the pieces can sometimes be welded together.
- Flanges are available in various styles, including slip-on flanges, lap-joint flanges, weld-neck flanges, and socket-weld flanges.
- Flanged valves find wide application across diverse industries, including oil and gas, chemical processing, power generation, and water treatment.
- Most flanged valves adhere to industry standards like ANSI/ASME B16.5, DIN 1092-1/ISO 7005, and SAE J518, which specify the dimensions, materials, and technical requirements for flanges used in various industrial applications.
- Flange ratings are typically designated by a numerical value, such as Class 150, Class 300, and Class 600; the higher numbers indicate greater pressure and temperature resistance.
Advantages
- Versatility: Flanged valves are versatile and can be used with different pipe sizes and materials, including steel, cast iron, and PVC. Also, they work well with hazardous fluids.
- Easy to remove: Flanged valves can be easily removed within the system without removing other components, which is difficult with threaded valves due to space constraints.
- Strength and durability: The flanged connection gives extra strength and durability to handle high pressure and temperature.
Limitations
- Cost: Installing flanged valves can be more expensive due to the need for bolt tightening and gasket replacement.
- Size: Flanged connections are typically larger and bulkier than other connections, which may not be ideal for space-constrained applications.
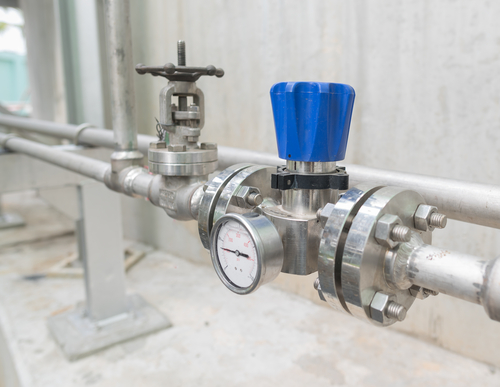
Figure 2: Flanged valves used in an industry
Threaded valves
Threaded valves, or screwed valves, have threaded ends for direct connection to compatible pipes or fittings. Threads are standardized to ensure compatibility and ease of maintenance. Common thread standards are BSP, NP, and UTS. Threaded valves are commonly found in plumbing systems, small-scale industrial processes, and residential applications.
Advantages
- Simplicity: Thread connections are simple and easy to install or replace, requiring no additional tools. Also, threaded connections need not be tightened as there are no bolts.
- Compact: They tend to be more compact and lightweight, making them suitable for tight spaces.
- Cost-effective: Threaded connections cost less as no multiple parts and flange configurations exist.
- Vibration tolerance: Threaded valves tolerate pump vibrations better as the threaded connection provides greater stability and reduces the risk of loosening under mechanical stress.
Limitations
- Limited stress tolerance: Threaded connections may not handle high pressures and temperatures, as well as other connection types.
- Corrosion: The threads in threaded valves are more susceptible to corrosion, making them difficult to remove and potentially weakening the connection.
- Potential leakage: Over time, threaded connections may experience wear or loosening, leading to potential leakage. Proper installation, periodic inspection, and maintenance are necessary to ensure the integrity of threaded valves.
Comparison table
Table 1: Flanged valves vs threaded valves
Parameter | Flanged valves | Threaded valves |
Connection method | Flanges with bolted joints | Threaded ends |
Application range | High-pressure and high-temperature applications | Low-pressure and low-temperature applications |
Installation complexity | More complex installation due to alignment and bolting | Simple installation by screwing onto compatible threads |
Maintenance | Easy removal and maintenance with bolted flange connections | Straightforward maintenance due to threaded connections |
Space requirement | Require more space for flanges and bolting | Compact design suitable for space-constrained installations |
Cost | Generally more expensive due to flanges and bolts | Cost-effective |
Leakage risk | Provides a tight and reliable seal with proper installation | Potential leakage due to wear or loosening of threaded joints |
Pressure and temperature | Suitable for high-pressure and high-temperature conditions | Not recommended for demanding pressure and temperature ranges |
FAQs
What is the difference between flanged valves and threaded valves?
Flanged valves have a flange connection that requires bolts for installation, while threaded valves have threads that allow for direct screwing onto the pipeline.
Which type of valve is more commonly used in industrial applications, flanged or threaded?
Flanged valves are more commonly used in industrial applications because they can handle higher pressures and larger pipe sizes.