Globe Valve Applications
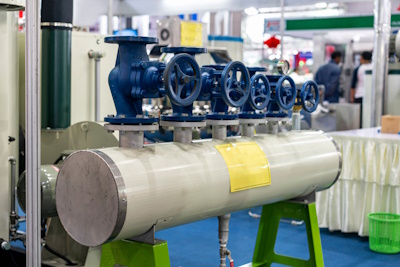
Figure 1: Various size metal globe valve for controlling the fluid in an industrial setting
Globe valves regulate flow with precision and are integral in applications requiring tight shut-off, throttling capabilities, and flow regulation. They are crucial for controlling fluid flow in pipelines, reactors, and other equipment. They also facilitate the isolation of pipeline sections and equipment for maintenance and repairs. This article explores the diverse applications of globe valves, highlighting their unique features and the reasons behind their suitability for specific roles in various sectors.
Table of contents
- Globe valve basics
- Globe valve features
- Water treatment industry
- Chemical industry
- Oil and gas industry
- Globe valves for steam
- Power generation industry
- Food and beverage industry
View our online selection of globe valves!
Globe valve basics
Globe valves are multi-turn linear valves. They are primarily employed to control the flow within a pipeline. A key advantage of globe valves is their superior ability to prevent leaks compared to other valve types. Globe valves are primarily utilized for throttling processes and can be regarded as general-purpose flow control valves suitable for high-temperature applications. Read our globe valve overview article for more details on the design and operation of globe valves.
Globe valve features
- Material versatility: Globe valves come in various materials like stainless steel and special alloys to handle the diverse operating conditions of power plants and oil industries, including high temperatures, pressures, and potentially corrosive fluids.
- Controllability: The throttling capability of globe valves allows for precise flow regulation, essential for maintaining optimal operating conditions in these complex systems. This is crucial for efficient heat transfer, pressure control, and process optimization.
- Leakage prevention: The tight shutoff design minimizes fugitive emissions, a growing concern in the power generation industry. This is particularly important for power plant systems to prevent CO2 leakage.
- Automated control: For automated process control systems commonly used in modern production industries, globe valves can be equipped with electric or pneumatic actuators. This allows for precise flow regulation and integration with control systems.
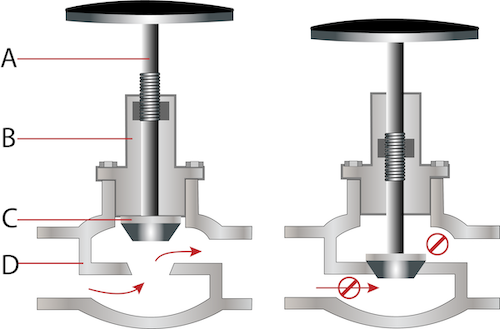
Figure 2: A globe valve in the open position (left), and in the closed position (right) with the valve stem (A), bonnet (B), disc or plug (C), and valve body (D).
Globe Valves for the water treatment industry
Globe valves play a vital role in water treatment systems, serving to regulate water flow, manage pressure, and prevent reverse flow. These valves are integral in various sections of water treatment plants, including the intake of raw water, chemical injection, and sludge disposal systems. Additionally, they are crucial for controlling water flow in distribution networks and pumping stations.
Globe valves are particularly valued for their fine control capabilities, allowing for the gradual adjustment of water flow, which is essential for maintaining the balance within treatment systems. Their specific use in this sector is largely due to their exceptional ability to modulate flow accurately, which is crucial for the various stages of water treatment, including filtration, chemical dosing, and sedimentation.
Other factors
- Cavitation resistance: Cavitation damage can occur in valves due to rapid pressure changes. In situations with high flow velocities, globe valves with cavitation-resistant designs can be employed to prevent erosion and maintain valve integrity.
- Double block and bleed (DB&B) isolation: For critical applications requiring absolute isolation, two globe valves with a bleed valve in between can be used in a DB&B configuration. This allows for safe draining and verification of isolation before maintenance work.
Globe Valves for the chemical industry
In the chemical sector, globe valves are essential for managing the flow of diverse fluids such as acids, alkalis, and solvents. They are extensively utilized in chemical processing plants to control chemical flow in pipelines, reactors, and storage tanks. Globe valves also regulate steam and gas flows in chemical processes.
Other factors
- Design: The strong-seated globe valve, known for its zero-leakage shutoff capability, is particularly well-suited for numerous applications in chemical plants. In such environments, it is advantageous to choose valves designed with thinner walls and lighter weights, making globe valves the preferred choices.
- Viscous or slurry flow: Globe valves can be configured with specific trim designs to handle viscous fluids or slurries containing suspended solids. This makes them suitable for applications like polymer production or handling catalyst mixtures.
- Specialty designs: For unique chemical processing needs, manufacturers offer globe valves with features like jacketed bodies for temperature control, bellow-sealed designs for extreme leak tightness, or fire-safe construction for enhanced safety in critical applications.
Globe Valves for the oil and gas industry
The oil and gas sector relies on globe valves for the management of crude oil, natural gas, and other fluid flows. These valves are employed in pipelines, refineries, and petrochemical plants, where they are valued for their capacity to handle high-pressure and high-temperature conditions. Globe valves also play a key role in isolating pipeline sections and equipment for maintenance and repairs.
Other factors
- Globe valves for offshore deep wells: In the oil and gas industry, globe valves are essential for managing high-pressure fluids in wellheads and production facilities. These valves are designed to withstand pressures up to 689 bar (10,000 psi), a requirement primarily for offshore deep wells. The selection of globe valves for pre-treatment processes in oil or gas production is critical due to their high-pressure handling and tensile strength. This is particularly important as raw petroleum streams often contain corrosive fluids like hydrogen sulfide, leading to the formation of sour gas. To mitigate the risks associated with sour gas, globe valves are manufactured from special materials and through techniques that ensure durability against such harsh conditions.
- Fire-safe construction: Safety is a top priority in the oil and gas industry. Globe valves can be designed with fire-safe features like self-sealing packing materials or metal-to-metal seating to maintain isolation even in case of a fire, preventing uncontrolled fluid release.
- Subsea applications: For subsea production systems, specially designed globe valves are available. These valves incorporate features like corrosion-resistant materials, self-lubricating packing, and pressure-compensating designs to function reliably in the harsh underwater environment.
Globe valves for steam
Globe valves are widely used in steam systems for various purposes, including:
- Isolation: They effectively isolate sections of a steam line for maintenance or repairs.
- Regulation: By throttling the flow path, globe valves are adept at regulating steam flow for pressure control or process needs.
- Bypass lines: They are frequently used in bypass lines around pressure regulators or other equipment, allowing for controlled flow during maintenance or emergencies.
Other factors
- Tight shutoff: Globe valves offer superior shutoff capability compared to other valves like gate valves. This is crucial in steam systems to prevent leaks and ensure complete isolation.
- Flow control: The internal design with a variable orifice formed by the disc and seat allows for precise flow control, essential for regulating steam pressure and optimizing processes.
- Pressure drop tolerance: Globe valves can handle significant pressure drops across the valve due to their robust construction and design. This is important in high-pressure steam systems.
- Material selection: For high-temperature steam applications, specific alloys like stainless steel are chosen for the valve body and internal components to withstand extreme temperatures and maintain structural integrity.
- Noise reduction options: Globe valves can be equipped with features like multi-stage trim or cage designs to minimize noise generated during throttling, which is a concern in some steam systems.
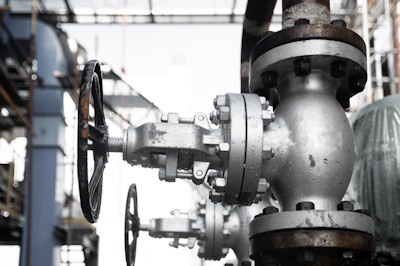
Figure 2: Steam globe valve in a factory
Globe Valves for the power generation industry
- Concentrated solar power (CSP): In CSP plants, globe valves are used for isolating and regulating the flow of heat transfer fluids like molten salts between collectors, storage tanks, and heat exchangers. Tight shutoff is crucial to prevent leaks and maintain thermal efficiency.
- Nuclear power: Within nuclear power plants, globe valves find application in auxiliary systems like condensate lines, feedwater lines, and various control loops. Their ability to handle high pressures and offer precise flow control is essential for safe and efficient operation.
- Geothermal power plants: In geothermal plants, globe valves are employed for regulating the flow of hot geothermal brine between wells, heat exchangers, and reinjection lines. Corrosion-resistant materials are necessary due to the often harsh geothermal fluid composition.
- Natural gas power plants with carbon capture and storage (CCS): Globe valves play a role in isolating and regulating the flow of captured CO2 within CCS systems. Tight shutoff is critical to prevent leakage of this greenhouse gas.
Other factors
- Special designs: For specific applications, such as high-pressure CO2 service in CCS systems, globe valves can be designed with features like special packing materials or anti-entrapment designs to ensure safety and reliability.
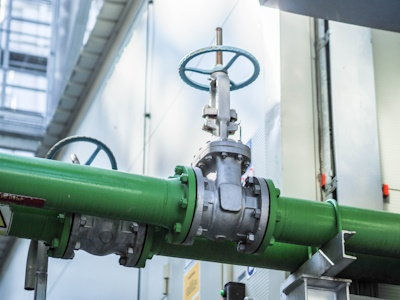
Figure 3: Manual globe valve in a power plant
Globe Valves for the food and beverage industry
In the food and beverage industry, globe valves are used to control the flow of liquids such as water, milk, and juices, as well as steam and gasses in processing plants.
- Product isolation: Globe valves excel at isolating processing lines and storage tanks for maintenance, cleaning, or product changeovers. Their tight shutoff capability minimizes product loss and potential contamination risks.
- Flow control: Precise flow regulation is crucial in various processes like blending ingredients, transferring liquids through pipelines, or controlling flow rates to heat exchangers or filling machines. Globe valves provide excellent throttling characteristics for achieving this control.
- Sanitary applications: In hygienic production environments, globe valves can be designed with sanitary finishes and crevice-free internal geometries to minimize areas where bacteria can harbor. This promotes better cleanability and reduces the risk of product contamination.
Other factors
- Design: One of the key design features that make globe valves suitable for the food and beverage sector is their smooth internal surfaces. This design minimizes the risk of contamination and facilitates easy cleaning, ensuring that the stringent hygiene standards of the industry are met.
- Materials: The materials used in globe valve construction, such as stainless steel, are selected for their corrosion resistance and non-reactivity with food products, further safeguarding product quality. By precisely controlling flow rates, these valves minimize the wastage of water and other valuable resources during production processes.
- Self-draining design: Certain globe valve designs incorporate self-draining features that minimize fluid pockets within the valve body. This helps prevent product stagnation and potential bacterial growth, especially important for hygienic applications.
- Specialized options: For specific applications, such as handling abrasive ingredients or chunky products, globe valves with special seat and disc materials can be used to enhance wear resistance and extend valve lifespan.