What Makes a Valve Fire-safe
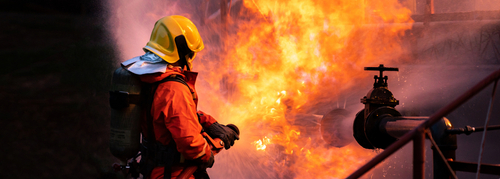
Figure 1: Fire in a natural gas station
Industrial valves must provide reliable fire protection in sensitive applications like refinery, oil and gas, and petrochemical industries. They should ensure a safe and dependable shut-off during fire incidents; hence, fire-safe design is crucial for these valves. This article explores the principle of fire testing and the design considerations for a fire-safe valve.
Table of contents
- Fire testing industrial valves
- The principle of fire-testing valves
- Fire-safe valve design
- Fire safe by design vs fire safe tested
- Certifications for fire-safe valves
- FAQs
View our online selection of valves!
Fire testing industrial valves
The American Petroleum Institute (API) developed fire tests for valves used in the oil and gas industries. These tests, such as ISO 10497, API 607, API 6FA, BS 5146, and BS 6755, have become accepted standards (discussed later). Many organizations develop their internal procedures for fire-safe valves based on these guidelines.
Valves that are considered 'fire-safe' must undergo rigorous tests. These tests vary in their methods and intensity and consider important factors such as how fires start and spread in specific situations, the type of fluid being used, the temperature during the peak fire, how tightly the valve should seal, and the valve's capabilities after a fire.
The principle of fire testing valves
According to a widely accepted firefighting strategy, a withdrawal and containment approach is implemented if a fire cannot be extinguished within 30 minutes. After 30 minutes, there is a significant risk of structural failures such as flange bolt failures, concrete eruptions, and pipe rack collapse. To align with this interval, the fire test lasts 30 minutes.
Fire tests are conducted to ensure that fire-safe valves can operate even after exposure to high temperatures for a specific duration. The principle of fire testing for valves is as follows:
- The valve is filled with water and surrounded by temperatures ranging from 750 - 1000 𐩑C (1382 - 1832 𐩑F) for 30 minutes while working under pressure. This exposes the sealing areas and seats to extremely high temperatures. The intensity of heat is continuously monitored using thermocouples.
- External and internal leakage across the valve is measured and compared with predetermined levels during the test. If the leakage exceeds the acceptable limits, there may be issues with the valve's integrity, which may not be suitable for fire safety applications.
- The valve is cooled down after the first test, and its pressure-containing capability is tested to ensure the seats, seals, and shell can maintain their integrity.
Fire-safe valve design
In certain situations, a valve might need to open or close when exposed to a severe fire. In those cases, manufacturers provide two options:
- Fire-safe valves are made of strong materials and seals that can handle the high temperatures of a fire without getting damaged.
- The fail-safe mode is usually achieved using springs or compressed air in pneumatic actuators. In the event of a power failure or loss of air pressure, the spring or compressed air drives the actuator to its fail-safe position.
- Electric actuators may include a battery backup that can provide power to move the actuator to its fail-safe position in the event of a power outage. Alternatively, some electric actuators use a mechanical spring mechanism similar to pneumatic actuators.
- Manual valves can be incorporated into a larger system with fail-safe mechanisms. For example, an alarm system could trigger in the event of a fire, alerting personnel to operate certain valves manually.
- A protective system that stops the actuator from getting too hot could lead to the seals breaking or the components getting distorted. The protective system prevents the actuator from getting too hot during a fire and aims to maintain the actuator within a safe temperature range. Doing so helps protect the valve's components and seals from damage or distortion due to extreme heat exposure.
The fire-safe design varies across manufacturers, some of which are listed below:
- Fire-safe butterfly valves often have three sealing layers. It uses a soft insert to create a tight seal under normal conditions. It has a metal-to-metal seal that closes tightly, even if the soft seal is damaged. These seals are made of specialized materials such as graphite or PTFE (polytetrafluoroethylene), which resist heat, fire, and chemical exposure. These valves typically work in temperatures ranging from -73 - 232 °C (100 to 450°F) and pressures up to 102 bar (1480 psi). They should meet the tight sealing standards set by MSS SP-61.
- Certain fire-safe designs have spring-driven actuators that automatically close the valve when a fire is detected.
- A floating-ball valve with PTFE seat rings is commonly used in fire-safe designs. Also, multiple sealing layers prevent external leakage at various points between the stem and gland flange, gland flange and body, and body and adapter. One layer comprises an o-ring, while the other comprises a graphite gasket. The secondary graphite gasket is a backup to prevent external leakage in case the o-ring sealing gets burnt.
Fire safe by design vs fire safe tested
While selecting a fire-safe valve, the terms 'fire-safe by design' and 'fire-safe tested' may sound similar but mean different things.
- Fire safe by design: A 'fire safe by design' valve is produced with fire safety in mind, meaning it is constructed using materials and design features that are intended to withstand high temperatures and prevent the spread of fire, but it hasn't undergone specific fire testing yet to validate its performance.
- Fire safe tested: A 'fire safe tested' valve may have been tested by the manufacturer or at a testing facility but lacks approval from a recognized third-party authority.
- Fire safe approved and certified: Valves labeled as 'fire safe approved and certified' have undergone thorough testing, approval, and certification by an authorized third-party organization. These certifications are based on widely recognized standards.
Certifications for fire-safe valves
- API 607/6FA: API 607 tests quarter-turn valves and valves with nonmetallic seating to ensure they can withstand fire. Alternatively, API 6FA is specifically for valves with metal seating.
- ISO 10497: The ISO 10497 certification provides a global standard for fire testing of valves, ensuring the valves can endure fire exposure and maintain tight shutoff. ISO 10497 certification is often required in industries where fire safety is critical, such as petrochemical, power generation, and chemical processing.
FAQs
How do I know if a valve is fire-safe?
Look for valves with certifications like API 607/6FA or ISO 10497. Also, check the valve design and ensure the materials are fire-proof.
What is a fire-safe ball valve?
Fire-safe ball valves prevent fire spread in explosive/fire-risk environments, tested to API 607, API 6FA, and BS 6755-Part 2.