How To Use a Bearing Puller
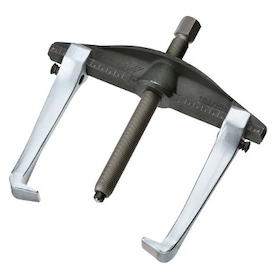
Figure 1: Manual bearing puller
A bearing puller is used to remove bearings, gears, or pulleys from shafts. A typical bearing puller has a forcing screw that is positioned on the end of the shaft and legs that circle around the back of the bearing. These are referred to as external bearing pullers, but internal (i.e. blind-bearing) pullers are also available. The applied force can be manual, hydraulic, or pneumatic. Even damaged, worn, or difficult-to-remove bearings are relatively easy to remove thanks to the specially designed claws, which fit around or inside shaft components. Read our bearing types article for more details.
Table of contents
- How do bearing pullers work?
- Bearing puller types
- Selection criteria for choosing the right type of bearing puller
- FAQ
View our online selection of bearing pullers!

How do bearing pullers work?
Used to remove bearings from shafts or housings, bearing pullers are available as internal pullers and external pullers. The most common type is an external bearing puller. The bearing or other components can be quickly and safely removed, as shown in Figure 2. By tightening the forcing screw (Figure 2 labeled D), the bearing (Figure 2 labeled B) will be pulled off the shaft (Figure 2 labeled C) through the force applied by the screw to the puller arms (Figure 2 labeledA).
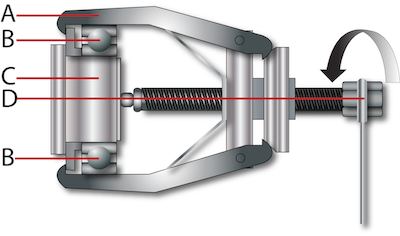
Figure 2: Bearing puller components: arms (A), bearing (B), shaft (C), and forcing screw (D).
How to use a bearing puller
Follow the below steps to use a bearing puller:
- Place bearing pullers: Depending on the type of part being removed, either place the puller around the part or place it internally.
- Adjust the bearing puller legs: Puller legs should fit tightly around or inside the part to be removed.
- Position the forcing screw: Manually turn the forcing screw clockwise until the screw touches the shaft. Ensure that the center of the screw is in the center of the shaft when adjusting the legs.
- Apply pressure to the forcing screw: Use a spanner or a socket wrench to turn the forcing screw slowly and carefully, or use hydraulic or pneumatic power to apply force.
- Remove part: Turning the forcing screw results in the part being pulled off the shaft.
Bearing puller types
External bearing puller
External manual bearing pullers are used when a bearing is mounted on a shaft. When tightened, the forcing screw pushes against the shaft's end, and the arms grip the bearing's outer diameter. A handle or wrench is used to tighten manually. With each tightening of the forcing screw, the jaws force the bearing along the shaft towards the puller.
These bearing pullers are usually used to remove small bearings. The arms can be reversed on some pullers to function as internal pullers or blind pullers. The most common type is manually operated, however, they can be operated with hydraulics or pneumatics
- External hydraulic bearing puller: Uses hydraulics to apply force to the forcing screw. Hydraulic bearing pullers are ideal for heavy-duty applications since they require little manual effort.
- External pneumatic bearing puller: Uses a pneumatic cylinder, actuator, and puller arms. By pressurizing the pneumatic cylinder with air, the forcing screw is forced against the shaft, unmounting the bearing. Suitable for heavy-duty applications.
Blind bearing puller
Blind bearing pullers are designed for bearings or components fitted within a housing with an opening in the inner diameter. A puller is inserted into the bearing's inner diameter and grips it using its jaws. The jaws on the puller can be expanded, similar to how an expansion bolt works, or clawed such as can be seen in figure 3. Using a slide hammer, which transmits impact force to the bearing without it striking the bearing itself, the bearing can be removed from the recess.
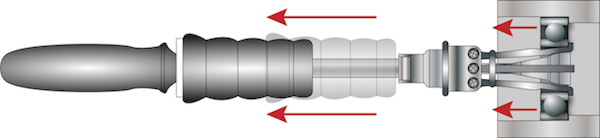
Figure 3: Blind bearing puller
Selection criteria for choosing the right type of bearing puller
- Internal or external bearing puller: The first decision is whether an external or internal bearing puller is needed. External bearing pullers remove bearings and other components mounted to a shaft. Internal or blind bearing pullers remove bearings or components mounted inside recesses. Examples are a wheel bearing seen in Figure 4 on the right or bearings mounted on a shaft such as in Figure 5 on the left.
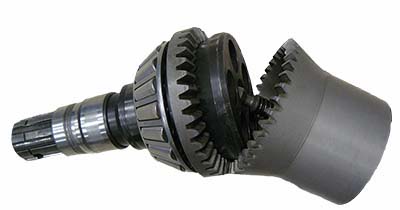
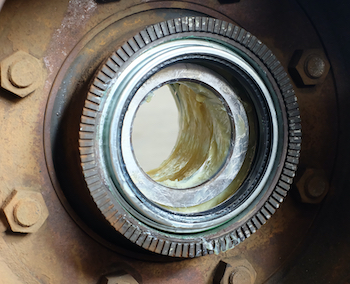
Figure 4: Tapered roller bearing on a shaft (left), and a Wheel bearing (right)
-
Actuator: The bearing puller and the actuator type depends mainly on the size of the bearing. A small bearing does not need a heavy-duty hydraulic puller, while a large diameter bearing will prove impossible to remove with a manual puller.
- A mechanical puller can be used to remove small bearings from the shaft. The arms should be applied to the inner ring. If the arms cannot be applied to the inner ring or an adjacent component, remove the bearing via the outer ring. If the puller is mounted on the outside ring, the bearing should not be reused as the possibilities for (invisible) internal damage are more common using this method.
- For large bearings, hydraulic or pneumatically assisted pullers should be used to remove them. Typically, these are available for bearings with outside diameters up to 500 mm.
- When a small bearing is mounted in a housing with a bore diameter ranging from 7 to 60 mm, an internal puller with a slide hammer can be used to remove the bearing. For larger bearings a hydraulic puller will need to be used.
- Maximum spread and maximum reach: The maximum spread is the width the arms can reach to fit around a bearing (B in Figure 5). The maximum reach is the distance between the end of the forcing screw and the point on the back of the bearing where the arms grip. Careful measuring is needed to ensure the correct bearing puller is specified for the application.
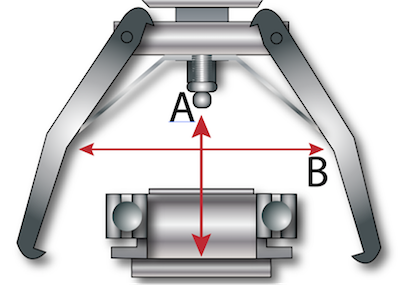
Figure 5: The maximum spread of a bearing puller (B) and the maximum reach (A).
FAQ
How to get a bearing off a shaft?
To get a bearing off a shaft, you will need to remove any retaining rings or locking devices, then gently tap the bearing with a rubber mallet or similar tool to loosen it from the shaft. You may also need to use a bearing puller or a hydraulic press to fully remove the bearing.